Rockwheel D20 for Rock Trenching: When is a Rockwheel the best call?
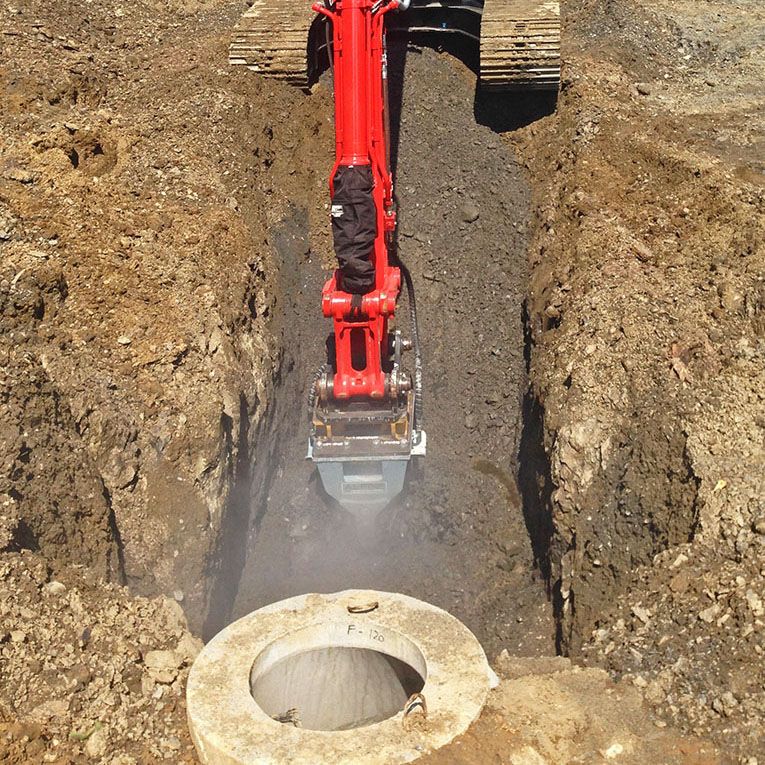
With regard to trenching in rock, a frequent question I get from customers and equipment dealers is "When do I use a Rockwheel vs. hammer or ripper bucket?" The answer is somewhat simple, the Rockwheel is the best option when the ground is too hard to rip with a bucket yet not so hard that a heavy hammer is required. There is a wide range of rock strength that falls within this Rockwheel Zone as the figure below illustrates
Of course we live in a world of nuances and gradients where the choice isn't always so easy so here are a few other pointers on when a Rockwheel should be the tool of choice for a rock trenching job:
- If the hammer is just punching holes in the rock, a Rockwheel is a better option.
- If noise and seismic disturbance (e.g. in residential area or near sensitive structures) is an issue, the quieter, smooth cutting Rockwheel is a better option.
- If you want to create reusable fill (2" and smaller rock cuttings) and not bring in a crusher, a Rockwheel is a better option
- If a flat trench bottom is required, the Rockwheel is a good choice. Even if you option to break out the rock with a hammer, the Rockwheel can be used to trim the walls and trench bottom.
- If the rock is highly fractured, the Rockwheel is an excellent choice because the many teeth on the drums will act as multiple rippers and excavator very rapidly.
- If a slot cut it desired, not the "V" trench one gets with a hammer, a Rockwheel is an excellent choice.
An Alpine D20 Rockwheel was recently employed for sewer line trenching in upstate, NY. The very hard shale was not ripable with the CAT 345 bucket with Tiger Teeth and because it was in a residential zone with concerns about noise, a hammer was problematic. Alpine installed a D20 Rockwheel on a new LinkBelt 250X4 (Tier 4). The LinkBelt was easily programmed to allow three speed & torque settings for the Rockwheel and the customer made rapid headway in the trenching job. When the rock was softer he went for faster drum RPMs and when harder rock was encountered, they went for lower RPMs but more torque in seconds. The result was a trench cut to the exact cross section without any overbreak or extra width at the top as is often the case when trenching with a hammer. Moreover, the milled rock made for perfect pipe bedding and backfill, saving the cost of bringing in this material.
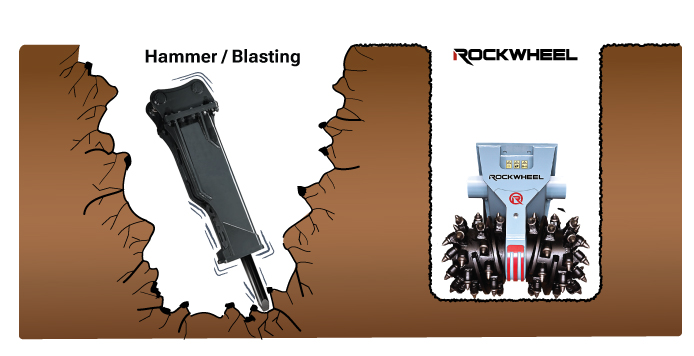