Rock Grinder Proves Faster Than Hammering In Chicago. Who? What? Why?
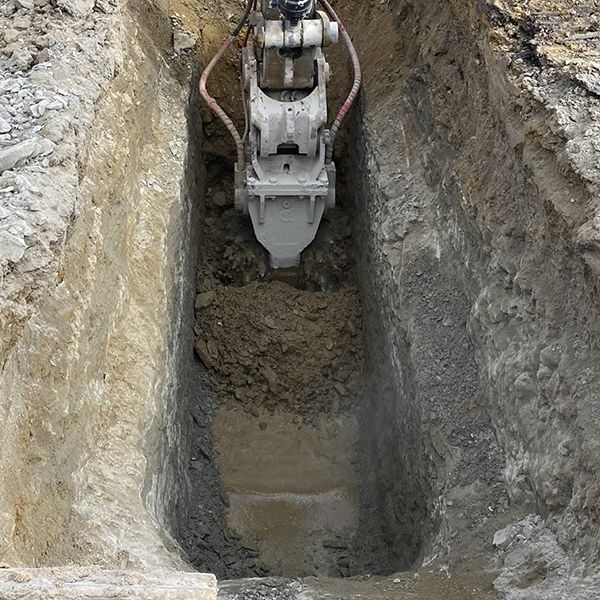
Frustrated by noisy tools, slow progress, and costly wear? RockZone Americas offers rock grinding machines that cut cleaner, quieter, and faster. Our attachments outperform hammer mills and help contractors tackle tough jobs with precision and efficiency.
Putting RockZone to the Test in Chicagoland Limestone
Scott Russ had seen Rockwheel drum cutters at trade shows and online, but he was unconvinced they could do more than the hydraulic hammers typically employed. J Russ and Company is a forward-thinking, full-service site civil contractor that has been working in the Chicagoland area since 1979. From their Lockport, IL headquarters, they specialize in mass grading, excavation, site utilities, and ground stabilization.
Scott contacted RockZone Americas (Bellefonte, PA) to learn more. While reviewing the job demands and available excavators with the RockZone team, it was determined that he needed a high power, aggressive Rockwheel for their Caterpillar 352 Next Gen (55t). Because RockZone Americas offers rent-purchase-option (RPO), he decided to rent the monster 300hp G60 twin drum Rockwheel to go after the notoriously challenging limestone in the Joliet, IL area, which can reach into the 20,000+ psi compressive strength range. The Rockwheel G60 is the only model in its class with gear reduction boasting up to 47,300 ft. lb of torque and nearly 40,000 lbs of pick force, so it offered an opportunity to directly assess rock grinding vs. impact hammering. The job, trenching in rock for the installation of sanitary sewer 3-10 feet deep, was already a handful for the 14,000 ft. lb. hammer, which was not meeting their production requirements, so why not take a chance on the newer method?
Key Features of Rock Grinding Machine Attachments
Rock grinders have conical carbide teeth installed at a 45° angle, which attacks the rock differently than a hammer. This angle of attack goes after the tensile and shear strength of the rock, which is much lower (~10-15% of compressive strength) than the compressive strength a hammer attacks. This is a result of the microscopic structure of rock: it contains microscopic cracks that are forced open and enlarged by tension and shear but which are forced closed by compression. (https://en.wikibooks.org/wiki/Historical_Geology/Physical_properties_of_rocks)
With approximately 60 teeth (depending on specific model) rotating continuously at a typical 60-65 rpm with very high torque, there can be 3000-4000 “bites” per minute. So, although an individual “bite” may not seem significant, the cumulative effect is remarkable! This also explains how a crushed stone product results from the grinding action and frequently this stone is reused onsite rather than hauled away as is the case with hammered rock.
How Our Rock Grinder Outperforms a Hammer
Precision over impact
Unlike a traditional hammer that relies on blunt force, our rock grinder delivers targeted, low-noise material removal. It’s engineered to grind, scale, and crush with control to reduce dust, minimize overbreak, and protect surrounding structures.
Versatile material processing
This rock grinding machine efficiently handles concrete, limestone, asphalt, and gypsum, turning tough rock into smaller pieces suitable for reuse. Whether you're trenching, excavating, or milling, the finished product is consistent, clean, and construction-ready.
Lower operating costs, easy maintenance
Fewer moving parts and durable construction mean less downtime and lower maintenance demands. Built for optimal performance and reliability, it helps crews operate more efficiently and manage tough jobs with confidence.
A smarter solution across industries
From construction to mining, our grinder is a high-performance solution for processing stone, gravel, glass, and more. It offers the power and precision needed to break through challenges and meet the demands of today’s job sites.
Onsite Performance & Benefits
On the job site, the result exceeded expectations with the Rockwheel G60 generating two major benefits: a significant increase in production compared to the hammer and the ability to reuse the 2-3 inch backfill created by the grinding process. Moreover, as the photos make clear, the precision of cut and absence of overbreak means no unnecessary excavation was done. He was very pleased with the G60 and may soon be adding another Rockwheel for a 40-ton excavator as the work of J Russ and Company expands. The RPO was a low-risk path to proving the effectiveness of the rock grinding approach. It allowed the use of the tool for an extended period on an active job with their own equipment and operators with the option, but not obligation, of converting to a purchase.
Rock Crusher Innovation & Industry Applications
When it comes to the Rockwheel drum cutters, as more units are successfully deployed nationwide, it’s hard to deny their advantages over hammers for many applications, especially rock trenching. From trenching to foundations and concrete removal to general rock excavation and beyond, Rockwheel offers a faster, higher precision, quieter, and more effective solution. RockZone Americas has a national rental fleet, a complete inventory of units and parts, nationwide service support, and the most experienced team in the business.
RockZone Americas: Powering Your Projects with Precision
At RockZone Americas, we manufacture high-performance rock grinders and rock crusher attachments that help our customers tackle tough jobs with confidence.
Our Rockwheel line—including twin-drum cutters, axial grinders, and trench cutter models—is engineered to deliver top results across concrete, asphalt, gypsum, limestone, and more. Whether you're renting or purchasing, we offer a range of models with the right specifications to match your equipment and project needs. For more information, visit or contact us directly at 814-900-6828 or email info@rockzoneamericas.com.